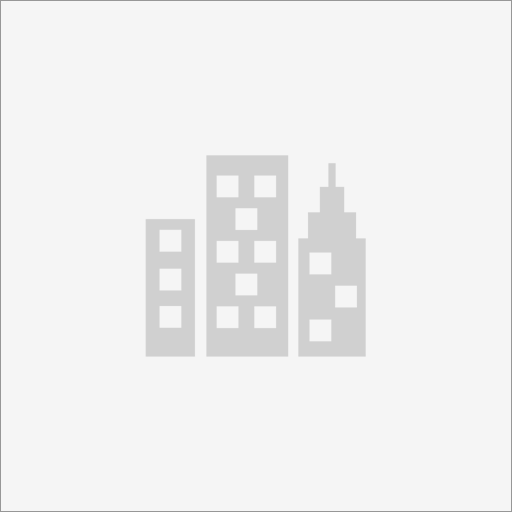
Confidential
QUALITY ASSURANCE SPECIALIST
LOCATION
Mount Pleasant, Iowa
COMPANY
At MackayMitchell, our customers and employees health and safety come first. We have been closely monitoring the events of the COVID-19 and the latest guidance from the Centers for Disease Control and Prevention (CDC). We have been deemed an essential business, therefore, we will continue to remain open and available to serve you during these difficult times. Please contact us via phone or you may place an order online.
JOB SUMMARY
The Quality Assurance (QA) Specialist is responsible for ensuring that the company’s quality assurance standards and procedures are met. The Quality Assurance Specialist will perform various QA-related tasks, which include tracking and reporting all activities, procedures and processes, developing auditing tools to improve the internal auditing process and conducting regular reviews and inspections to ensure employee adherence to quality standards. The Quality Assurance Specialist is expected to assist with the creation of company policies, procedures and processes and to conduct quality training sessions. The role will be charged with contributing to the development of a complete QA program that not only safeguards product quality, but also fosters a culture in which all employees are actively engaged.
SALARY
$70,000 – $90,000 (commensurate with experience)
RESPONSIBILITIES
- Assist with development, implementation, management and integration of a QMS for manufacturing plant
- Manage day-to-day activities and performance of Quality Control (QC) Machine Operators (one (1) per shift); provide learning and coaching opportunities to achieve quality standards and compliant operations
- Perform root cause analysis and other problem-solving activities to identify effective corrective actions and process improvements; provide feedback to manufacturing in regard to the impact of quality errors, particularly with key accounts
- Collaborate as needed with vendors, Sales, Account Managers (CSR’s) and Plant Managers to resolve quality issues by developing, coordinating, communicating and executing plans that meet objectives/standards
- Achieve quality assurance operational objectives by contributing information and analysis to strategic plans and reviews; prepare and complete action plans
- Complete audits; design, implement and document procedures for process control, process improvement, inspection, calibration and testing
- Monitor and validate quality processes and systems by establishing and implementing metrics
- Monitor compliance; conduct audits and complete/publish/analyze reports
- Drive plant accountabilities in the areas of: tracking vendor performance, resolution and disposition of customer complaints, investigation of critical quality defects in in-process and finished products, generation and analysis of quality data and reports
- Conduct research to identify industry trends and issues that may impact the organization’s operations
- Recommend changes to processes to improve product quality
- Train employees on quality control protocols to ensure compliance with standards
- Provide “on call” support (via phone) to plant personnel in response to critical quality issues
- Pursue continuing education, as applicable, in new solutions, technologies and skills
- Perform all other duties as assigned
QUALIFICATIONS
- 2+ years in a quality or quality control role
- Experience with audits and auditing a Quality Management System (QMS)
- Experience managing quality control technicians/operators preferred
- ISO 90001 or CQA certification preferred
- Lean manufacturing experience a plus
- Strong computer skills (e.g., Excel Pivot Tables, etc.)
- Highschool Degree
MacKayMitchell Envelope is an Equal Opportunity Employer and is committed to diversity in our workforce. EOE/M/F/D/V